
After all the colors have been added and the design is finally ready, the garment is then be heated to dry the ink. Hence, cotton is a much better material than Polyester as the former is made of fibrous material while the latter is made of a smoother material. The inks then bind directly with the textile fibers. These colors are applied according to their order in the acronym, to come up with all the colors in the digital design. This model is also referred to as four-color processing as it uses the combinations of the four ink colors. This model comprises of four colors namely cyan, magenta, yellow, and black- the key color.

Generally, the process for translating the colors from the digital image into ink to print onto the garment depends on this model. Thus, one can expect to have a high-quality vibrant colored print that is durable and long lasting. The fusing agent enables the ink to stay on the fabric permanently after the garment is printed with the design and pressed. The characteristic to chemically react with the inks for easy drying and curing.ĭTG inks contain what are known as fusing agents. This helps it to achieve the following: A smoother substrate by laying down loose fibers.Ī firmer bond between the textile fibers and the pigmented inks. Unlike the traditional printing methods, DTG can also print a single shirt for minimal cost - short runs!.īefore printing, the garment should undergo pre-treatment using a pre-treatment sprayer or machine ( PTM ). Since this process is digital, one can expect a sharper and higher resolution print than competing technologies such as screen printing and others. Then, the print head jets or sprays the garment with the DTG printer inks.
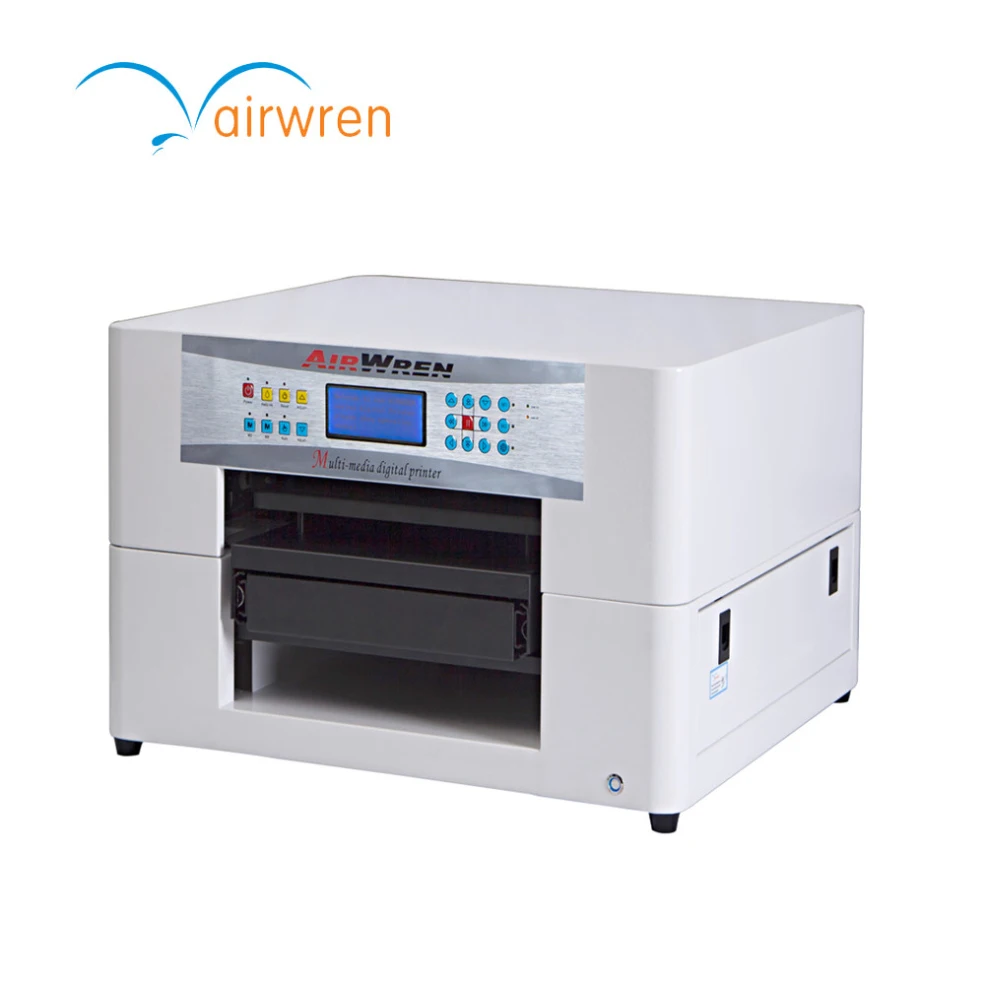
Direct-to-garment (DTG) printers are usually designed with a platen to firmly hold a garment in place.
